What does fabric abrasion resistance stand for?
Abrasion resistance plays a very important role in the performance and safety of protective clothing. During use, the fabric experiences rubbing, contact stresses, and potential snagging that can decrease its barrier properties.
Good abrasion resistance ensures that the protective clothing maintains its barrier capabilities even after some wear and tear. This is crucial for preventing hazardous substances like chemicals, liquids, or biological agents from penetrating through and potentially harming the wearer. High abrasion resistance improves the durability and extends the usable lifespan of the garments.
How to test fabric abrasion resistance?
Test results are influenced by various factors like the type of fabric, abrasive surface used, the force
applied during testing, and the endpoint criteria. Relevant safety regulations also vary based on the
data obtained from the test. For example, EU standards has specific regulations for chemical
protective clothing materials. These regulations classify materials into six different levels based on
the results of abrasion resistance testing.
There is a common standard taken to judge the ability of abrasion, . It is part of a larger standard called “ISO 12947: Textiles – Determination of the abrasion resistance of fabrics by the Martindale method”. Specifically, it simulates real-life wear and tear on a fabric sample through a controlled abrasion process.
For this test, a special piece of equipment called a Martindale tester is used. It applies a controlled pressure force and rubbing motion to a fabric sample. A standard abrasive material, typically a woven cotton fabric or sandpaper with specific specifications, is used.
The tester automatically performs a series of rubbing cycles on the fabric sample. It continues for a pre-determined number of cycles (based on the expected wear and tear) or until a set endpoint is reached (e.g. two threads breaking).
After testing, the fabric sample is carefully inspected visually for signs of wear and damage, like pilling, tearing, breaking, fraying, holes or formation of small fiber in surface texture. Additional measurements may also be taken, such as changes in fabric thickness, weight loss, or liquid penetration caused by the abrasion.
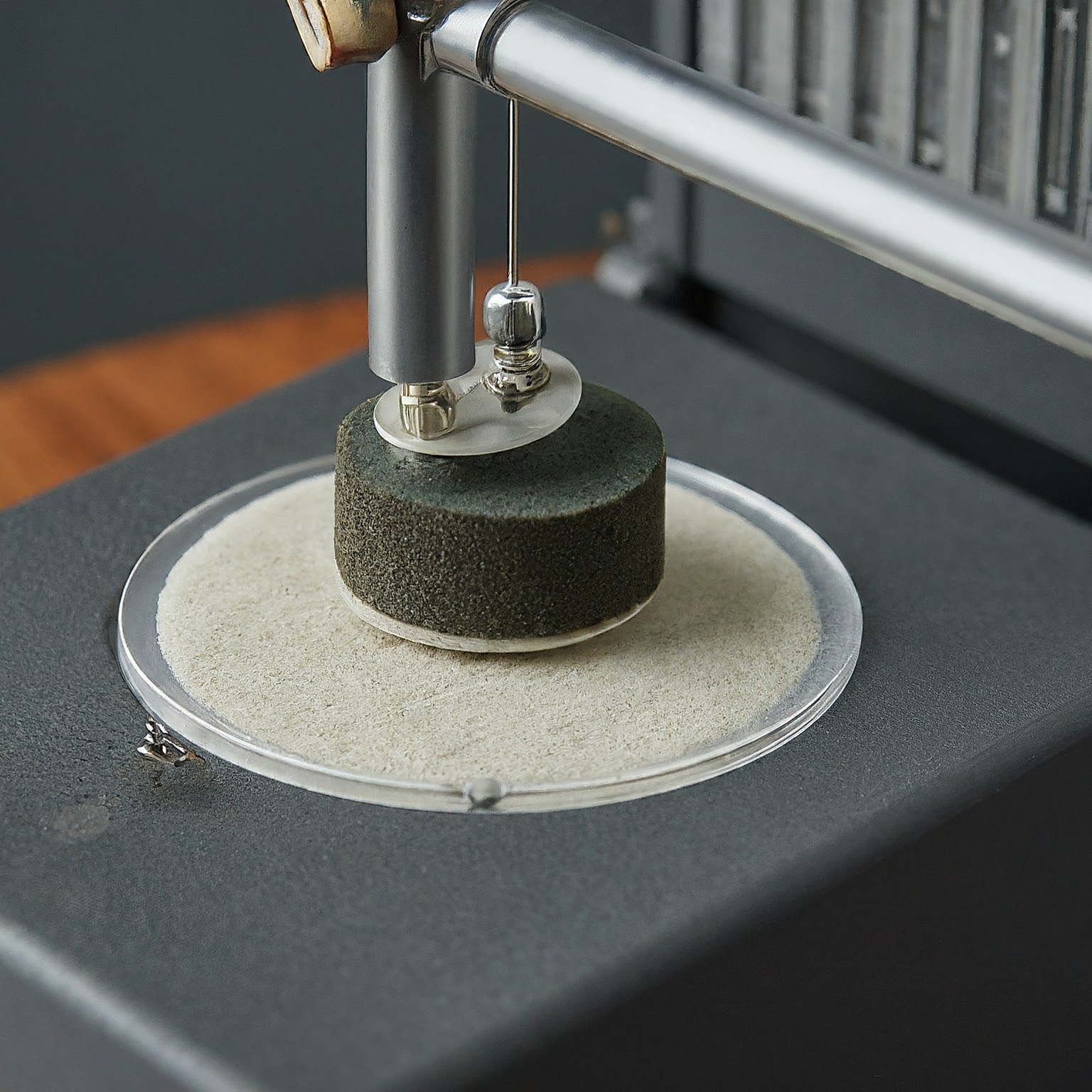
Pic 1: The chosen abrasive surface will push and rotate fabric sample to simulate abrasive situation.
Why fabric abrasion resistance is important for protective clothing?
Abrasion resistance is very important for protective clothing fabrics for several key reasons:
1. It ensures the fabric of protective clothing does not lose its protective barrier capabilities against harmful environment, include dust, liquid, germs, viruses and other infectious agents, even after extended wear and use.
2. It allows the protective clothing to have a longer usable service life. Fabrics undergo stresses from rubbing during dressing/undressing, movement, or decontaminations. High abrasion resistance means the base material can withstand damages during use and reduces the need for frequent replacements.
3. It improves safety of front-line worker. In high-risk work settings, protective clothing may encounter sharp tools, metal edges or abrasive surfaces. Excellent fabric abrasion resistance minimizes chances of the garment’s integrity being compromised from such contact hazards.
4. It helps meet safety standards. Standards like EN 14325:2018, the test method and performance classification requirement for protective clothing materials, not only change abrasion test method from EN 530 to ISO 12947-2, also request a minimum abrasion resistance level to ensure reliable protection across different use conditions.
Beyond ensuring a protective clothing’s lifespan, the abrasion resistance testing simulates real-world wear scraping against rough surfaces or falls. This helps predict how well the front-line wearers during accidents, ensuring their continued safety throughout use.